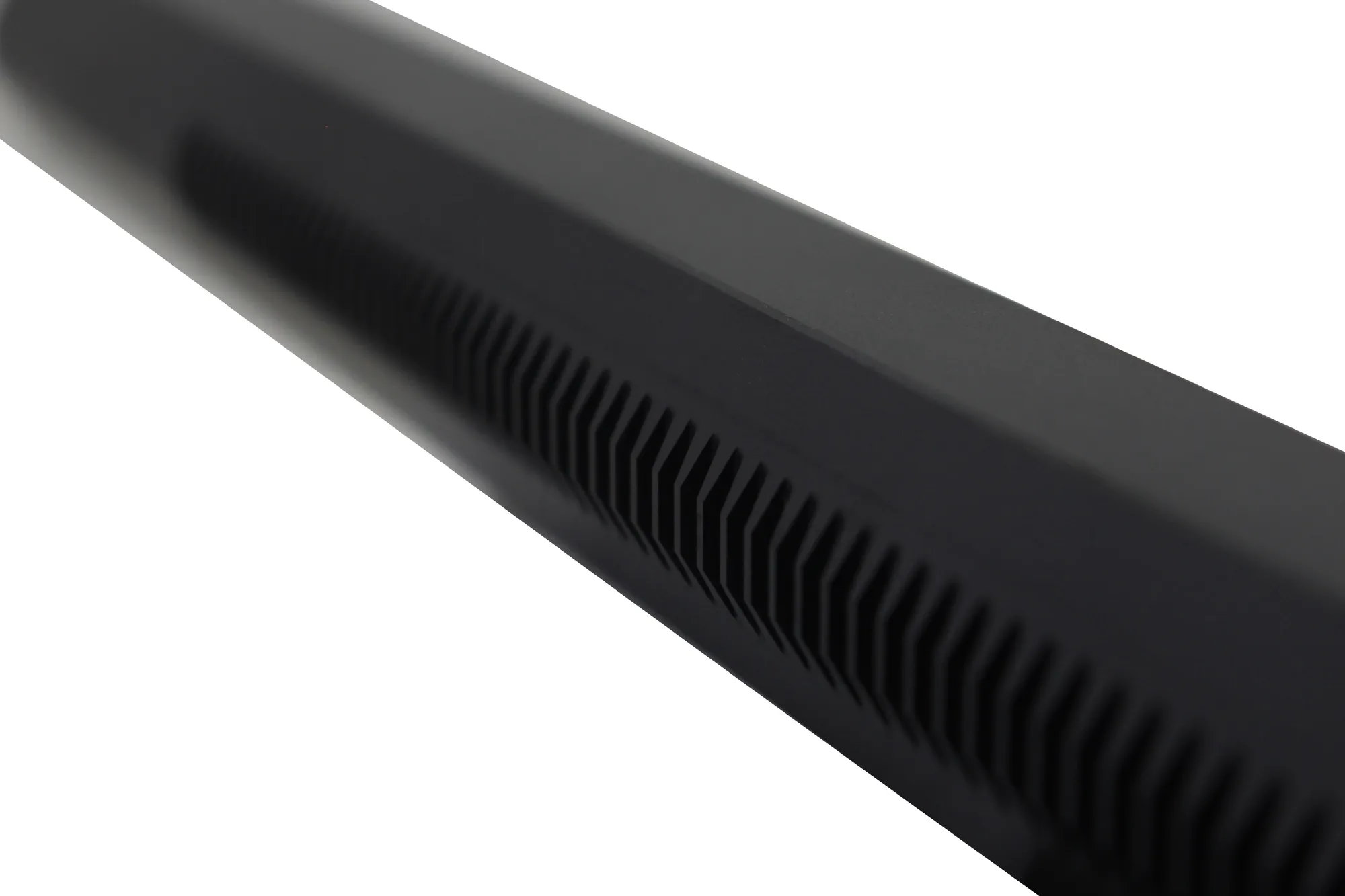
What is Nitrocarburizing?
Nitrocarburizing is a surface / case hardening process that strengthens the outer layer of a component. It creates a hard, wear-resistant shell on the surface. Importantly, it does not significantly affect the core hardness or dimensions of the workpiece.
What Are The Advantages of Nitrocarburizing?
- Wear & Galling: Nitrocarburizing significantly reduces wear and galling by increasing surface hardness and reducing friction and adhesion by up to 60%.
- Lubricity: It enhances lubricity due to the ceramic-like properties of the iron-nitride surface, making it an ideal choice for applications where oil or grease may not be an option.
- Corrosion Resistance: The presence of an iron nitride compound layer and a black oxide layer greatly improves corrosion resistance.
- Surface Roughness (RA) / Finish: While nitrocarburizing may slightly roughen the surface if pre-nitride RA is <32µin (0.8µm), it can be easily restored to pre-nitride finish through processes like glass bead polishing (QP) or Scotch-Brite pad polishing, which we do in-house. Pre-nitriding surface finishes >32µin (0.8µm) will likely not see an increase in surface roughness. Surface finishes as low as 2µin (0.05µm) can be restored after nitriding.
- Black Finish: Nitrocarburized parts have an attractive black finish that can replace paint or be polished to a jewelry-like shine, making nitriding ideal for various applications, including architectural pieces and firearms.
- Distortion Free: Nitrocarburizing typically does not cause distortion, preserving the workpiece's original shape and dimensions.
- Dimensional Stability: Surface growth is minimal, typically ranging from 0.0001" to 0.0003" (per surface), making it possible to finish-machine workpieces to final dimensions before nitrocarburizing.
- No Further Machining Required: Workpieces are almost always finish-machined to their final dimensions before nitrocarburizing.
- Fast Cycle Time: Nitrocarburizing offers quick turnaround times, with an average of 4-5 days. Expedited options are available for even faster service.
- Stress Relieving: In some cases, nitrocarburizing can serve as stress relief as in the example for heat-affected zones in welded assemblies (weldments).
- Wide Range of Workpiece Sizes: Nitrocarburizing can accommodate small parts as well as larger workpieces.
- Low Scrap Rate: Unlike conventional heat treating (quench & temper, carburising) the likelihood of scrapping workpieces due to fixturing or processing errors is minimal, resulting in an ultra-low scrap rate.
- Eco-Friendly: Nitrocarburizing is an environmentally friendly alternative to processes like chrome plating.
- Versatile Alternative: Nitrocarburizing can replace various processes, including: Conventional heat treating, carburizing, chrome & nickel plating, induction hardening, paint, ceramic coatings, cerakote, boron-nitride spray coating.
- Low Minimum Fee: Unlike conventional heat treating and other processes, the nitriding process offers a low minimum fee of $100.00 for our services.
- Safety: Unlike conventional heat treating & gas nitriding, our salt bath nitriding process poses no risk of chamber explosion or the release of hazardous gasses.
What Are The Disadvantages of Nitrocarburizing?
- Too Good: Nitrocarburizing's effectiveness may reduce the need for repeat work, impacting aftermarket services.
- Tempering: The process temperature (approximately 1055°F) can temper certain hardened materials, especially if they were originally tempered at lower temperatures.
- Stress Relieving: Residual stresses may be relieved (causing distortion) in some workpieces, particularly those made from cold-worked materials.
- Thin Parts: Very thin parts or crosssections thereof (less than 0.0010"/0.0254mm) may become embrittled due to through hardening, which can be mitigated by reducing process time.
Surface Growth
Surface growth typically ranges from 0.0001" to 0.0004" per surface (0.0002" to 0.0008" across the diameter). The degree of surface growth depends on the material. Approximate values are as follows:
- 0.0004” for steels (e.g. 1018)
- 0.0002” for low-alloy steel (e.g. 4140)
- 0.0001” for stainless steels (e.g. 303)
Please allow for the appropriate surface growth induced by nitriding. Multiple the values above x2 for diameter growth.
Surface Finish: Does Nitriding Affect Surface Finish?
Nitriding can increase the surface roughness (RA) / finish of a workpiece if it is under a 32µin (0.8 Ra µ-m). Assume that any finish from 1-32 (0.025-0.8 Ra µ-m) will be increased to 32 Ra µ-in (0.8 Ra µ-m). The surface finish is easily restored to a 16 Ra µ-in (0.4 Ra µ-m) by glass bead polishing (QP), after nitriding, we do this internally. Finer finishes can be restored down to a 2 Ra µ-in (0.05 Ra µ-m) by polishing with 800 grit (light grey) Scotch-Brite pads (often done on a lathe for seal surfaces) or can be done by other means. If corrosion resistance is important, the workpieces should be black oxidized again after polishing (QPQ), we do this internally.
Stress Relieving: Does the Nitriding Process Temperature Stress Relieve?
Residual stresses from machining, welding, forming, and some materials like cold worked steels, may stress relieve during nitriding as the process temperature (~1055°F) is close to the temperature used to stress relieve steel workpieces. If you believe you can safely stress relieve your workpiece, it should be safe to nitride it in this regard. Although rare, we have seen some workpieces distort owing to the nitride process temperature relieving stress.
Tempering: Will Nitriding Tempering My Parts?
The nitrocarburizing process temperature is 1055°F (565°C) and may be hot enough to temper some hardened materials, especially if the final tempering/hardening temperature was less than 1055°F. Example: 4140 quench & tempered to 50HRC will be tempered to a core hardness of 36HRC but the nitride case will be ~65HRC (at the surface).
Corrosion Resistance: How does Nitriding Effect Corrosion Resistance?
- Carbon, low-alloy & tool steels: Experience greatly improved corrosion resistance.
- Cast Irons: Show modest improvement in corrosion resistance, with graphite nodules / inclusions creating un-nitrided areas where corrosion may begin.
- Corrosion resistant stainless steels (e.g. 300 series): Will experience decreased corrosion resistance due to the removal of chrome-oxide passivation layers during nitriding. The QPQ process can improve corrosion resistance (compared to regular nitriding) but may not match the stainless steel's original corrosion resistance.
Case Depth: How deep does the Nitriding go?
Total Case Depth:
- Definition: The distance measured perpendicularly from the surface inwards to where the hardness of the nitrided case is indistinguishable from the core material hardness.
- Material dependent; extends up to 0.030" for steels (1018), 0.020" for low-alloy steel (4140), and 0.003" for stainless steels (303 & 17-4).
Effective Case Depth:
- Definition: The distance measured perpendicularly from the surface inwards to where the hardness of the nitrided case drops to 50HRC.
- Material and core hardness dependent; applicable to hardenable materials that have been through-hardened (e.g. 4140HTSR & 4140Q&T). Effective case depths for 4140, for example, can range from 0.002" to 0.005" depending on core hardness and nitride bath soak time.
We have an extensive material reference table developed with over a decade of inhouse lab test results. Using this reference table we can estimate expected surface hardness, case depth, compatibility with prior heat treatment, and much more.
Masking: Can you selectively mask off certain features of a part?
Salt bath nitrocarburizing typically doesn't require masking. Unlike gas nitriding, which can through-nitride thread crests, salt bath nitrocarburizing doesn't face the same masking requirement & cost. If you require selective treatment, you can leave extra material on features you do not want nitrided, then finish machine after nitriding.
Materials: What materials can be Nitrocarburized?
Most ferrous (iron-based) metals are suitable for nitrocarburizing, including:
- Low and Medium Carbon Steels: These are among the most common materials processed using liquid salt bath nitrocarburizing. Examples include AISI 1018, 1020, and 1045 steels.
- Alloy Steels: Various alloy steels, including those with higher levels of carbon and additional alloying elements, can undergo nitrocarburizing. Examples include AISI 4140, 4130, 4145, 4340, 4320, and 8620.
- Tool Steels: Tool steels are often treated with nitrocarburizing to enhance their wear resistance and durability. Examples include A1, A2, O1, O2, S7, H13 and D2 tool steels.
- Cast Iron: Gray cast iron and ductile cast iron are compatible with nitrocarburizing, with the process providing increased wear resistance and improved surface hardness. E.g. Ductile Iron, Grey Iron, Nodular Iron.
- Stainless Steels: Stainless steel alloys can be nitrocarburized to improve wear resistance but the effect on corrosion resistance varies widely. Common examples include 303, 304, 316, 416, 17-4 PH and 15-5 PH stainless steels.
- Sintered Materials: Powder metallurgy components, such as those made from sintered or 3D printed steel, can undergo nitrocarburizing to improve surface properties.
- Nickel-Based Alloys: Some nickel alloys can also be nitrided including Inconel 718
What is the difference between Q, QP, QPQ?
While all three processes provide similar surface and case hardness/depth, they differ in terms of surface finish and corrosion resistance:
- Q (Quench): Adds corrosion resistance by quenching the workpiece into an oxidizing salt bath after nitriding, producing a black oxide finish.
- QP (Quench Polish): Improves surface finish, resulting in a shinier, more lustrous appearance. Surface roughness is restored to the original machined (pre-nitride) finish. QP may reduce corrosion resistance, especially on certain stainless steels.
- QPQ (Quench Polish Quench): Combines surface finish improvement of QP, and adds corrosion resistance restoration in the oxidizing bath. QPQ offers the best corrosion resistance, especially on stainless steels.
Welding after nitriding?
Welding can be performed on nitrided parts after preparing the weld area with a grinder. Typically, about 0.010" (0.25mm) of material should be removed for successful welding.
Re-Nitriding?
Yes, workpieces can be re-nitrided, although the finish may appear brown after a second nitride, especially if the first nitride was a Q process. To achieve the best aesthetic, polishing or aluminum oxide blasting can prep the surface for re-nitride. After re-nitride we may need to polishing the parts for aesthetics purposes.
Pre-Nitrocarburizing Surface Condition Requirements:
Bear in mind that nitriding is a full immersion into a 1055°F molten salt bath. Workpieces should be free of scale, rust, excessive oil/grease, machining chips in holes, and non-ferrous materials. Various cleaning methods are available, including aluminum oxide blasting, to prepare workpieces.
Unique Applications & Better-Than-Expected Results:
- Welding Jigs: Nitrocarburizing welding jigs can effectively prevent weld spatter from sticking.
- Engine Crank Shafts: Nitrided crankshafts can virtually eliminate wear, reducing the need for rebuilds.
- Heavy Equipment Attachment Pins: Nitrided pins last 2-4 times longer than traditionally induction-hardened pins, and they resist rust.
- Diesel Engine Exhaust Brakes: Nitrided exhaust brakes made from lower-grade iron and steel exhibit excellent longevity and lubricity properties.
- Firearm Barrels: Nitrided barrels experience less fouling, copper buildup, and extended round counts before cleaning is required to restore accuracy.
- Automotive Brake Rotors: Nitrided brake rotors last longer and resist rusting, with the added benefit of maintaining a blackened appearance where the pads contact the rotor.
Do you have any tips regarding machining?
- Profile thread crests (don't leave them pointy/sharp) to avoid major diameter growth during nitriding, and chipping during subsequent polish (if QP).
- Avoid or remove burrs on corners and other features to maintain surface quality.
- Chamfer edges or better yet, replace corners with radii of at least 0.2mm.
Why is there a brown color on my parts?
Some nitrocarburized parts may exhibit brown color, primarily in the case of Q-processed parts. This coloration results from the oxidation process and can be minimized but not entirely avoided in every case. Brown can be easily removed by QP or QPQ processing.
Applications of Nitrocarburizing:
Nitrocarburizing can benefit a wide range of products, including:
- Bushings: Nitriding is employed to improve the wear resistance and extend the service life of bushings used in various mechanical systems, including automotive parts and industrial machinery.
- Shafts: Shafts used in machinery and automotive applications benefit from nitriding to increase their hardness and resistance to wear, reducing the risk of premature failure.
- Wear Sleeves: Wear sleeves, which are used to protect shafts and extend their lifespan in dynamic applications, can be nitrided to enhance their wear resistance and surface hardness.
- Firearms Components: Nitriding is widely used in the firearms industry to improve the performance and durability of components like barrels, bolts, actions, triggers, and other critical parts, reducing friction and enhancing corrosion resistance.
- Die Sets (Bending, Brake, Stamping): Die sets used in metalworking and forming processes, such as bending, brake forming, and stamping, are nitrided to increase their wear resistance and extend their operational life.
- Ball Joints and Tie Rods: Automotive and industrial ball joints and tie rods undergo nitriding to improve their resistance to wear and corrosion, ensuring smoother and more reliable operation.
- Injection Molds: Nitriding is commonly applied to injection molds used in plastic and rubber manufacturing to enhance their wear resistance, reduce maintenance, and improve product quality.
- Gears: Nitriding is used to harden and improve the wear resistance of various types of gears, including those used in automotive transmissions and industrial machinery.
- CNC Machining Fixtures: CNC machining fixtures, used to hold workpieces during machining operations, can be nitrided to increase their durability and resistance to wear in high-precision manufacturing processes.
- Engine Valves: Engine valves in internal combustion engines can be nitrided to improve their wear resistance, reducing the risk of valve seat and guide wear.
- Rocker Arms: Nitriding enhances the wear resistance and performance of rocker arms in internal combustion engines, reducing friction and extending their operational life.
- Crankshafts: Crankshafts, critical components in engines, undergo nitriding to improve their fatigue resistance, wear resistance, and overall durability.
- Extrusion Dies: Dies used in the extrusion of materials like plastics, rubber, and aluminum can benefit from nitriding to improve wear resistance and extend their service life.
- Tooling: Insert holders used in cutting, milling, and forming operations, such as lathe tools, milling cutters, and punches, can be nitrided to increase their wear resistance and tool life.
- Piston Rings: Nitriding can improve the wear resistance of piston rings, reducing friction and enhancing their longevity in internal combustion engines.
- Hydraulic Cylinder Rods: Components like hydraulic cylinder rods can be nitrided to improve their resistance to wear and corrosion, ensuring smooth and reliable operation.
- Springs: Nitriding can be applied to various types of springs, such as valve springs in engines or suspension springs in automotive applications, to enhance their fatigue resistance.
- Bearings: Bearing assemblies, including races and balls, can be nitrided to improve their performance and longevity.
- Screws and Fasteners: Nitriding can be used to improve the wear resistance and corrosion resistance of screws, bolts, and other fasteners.
- Extruder Screws: Screws used in plastic extrusion machinery can undergo nitriding to resist wear and maintain dimensional stability over time.
- Mold and Die Inserts: Inserts used in plastic injection molding and die-casting molds can be nitrided to extend their service life and maintain product quality.
- Firearm Components: In addition to barrels, bolts, and actions, other firearm components like trigger assemblies, hammers, and sears can be nitrided to enhance their durability and reduce friction.
- Motorcycle Components: Motorcycle parts such as camshafts, transmission gears, and crankshafts can undergo nitriding to improve their performance and longevity.
- Oil & Gas Industry Components: Various components used in the oil and gas industry, including drill bits, valves, and connectors, can benefit from nitriding to resist wear and corrosion in harsh environments.
- Compression Cylinders for Various Engines: Compression cylinders used in air and gas engines, including internal combustion engines, can be nitrided to enhance their resistance to wear and corrosion, ensuring reliable and efficient operation.
- Agricultural Food Processing: Plant processing equipment such as the trimming blades of medical marijuana trimming machines benefit greatly from nitriding.
In summary, nitriding is a valuable surface treatment process employed across various industries to improve the hardness, wear resistance, and overall performance of ferrous components. Whether in automotive, manufacturing, aerospace, or firearms applications, nitriding helps extend the service life of critical parts and reduces the need for frequent maintenance and replacement.
Q vs QP vs QPQ Application Table
(Standard process)
Polish + Quench
Reduces Friction & Adhesion by up to 60%
Black Oxide (Quench) for Corrosion Resistance & Aesthetics.
Nitriding can increase RA up to ~32µin (0.8µm) total
QP restores RA to ~8-16µin (0.2-0.4µm)
RA can be restored to ~2µin (0.05µm) by hand polishing or other means.
Some material may be aesthetically affected by brown/red iron oxides (particularly stainless steels and cast iron)
Very high quality & consistent appearance from part to part & batch to batch.
Polishing removes brown oxides and other surface contamination & visible defects.
(Compared to Raw / un-Nitrided Material)
Martensitic stainless steels: Moderate increase
Nodular irons: Slight increase
Precipitation hardened stainless steels: Unchanged
Ferritic & Austenitic stainless steels: Decreased
Martensitic stainless steels: Same as Q
Nodular irons: Same as Q
Precipitation hardened stainless steels: Reduced compared to Q
Ferritic & Austenitic stainless steels: Further reduced compared to Q
Martensitic stainless steels: Likely better than Q
Nodular irons: Same as Q
Precipitation hardened stainless steels: Likely better than Q
Ferritic & Austenitic stainless steels: Significantly better than Q
Components with high-spec aesthetic requirements. E.g.: Firearms, tools, etc.
Everything else if the additional cost is worth it.
1 55-60HRC for Carbon Steels, 60-70HRC for Low-alloy Steels, 70HRC+ for Stainless Steels
2 Nitriding is not expected to increase surface roughness (RA) where the starting roughness is >32µin (0.8µm)
3 Up to ~400hr ASTM B117 salt spray test