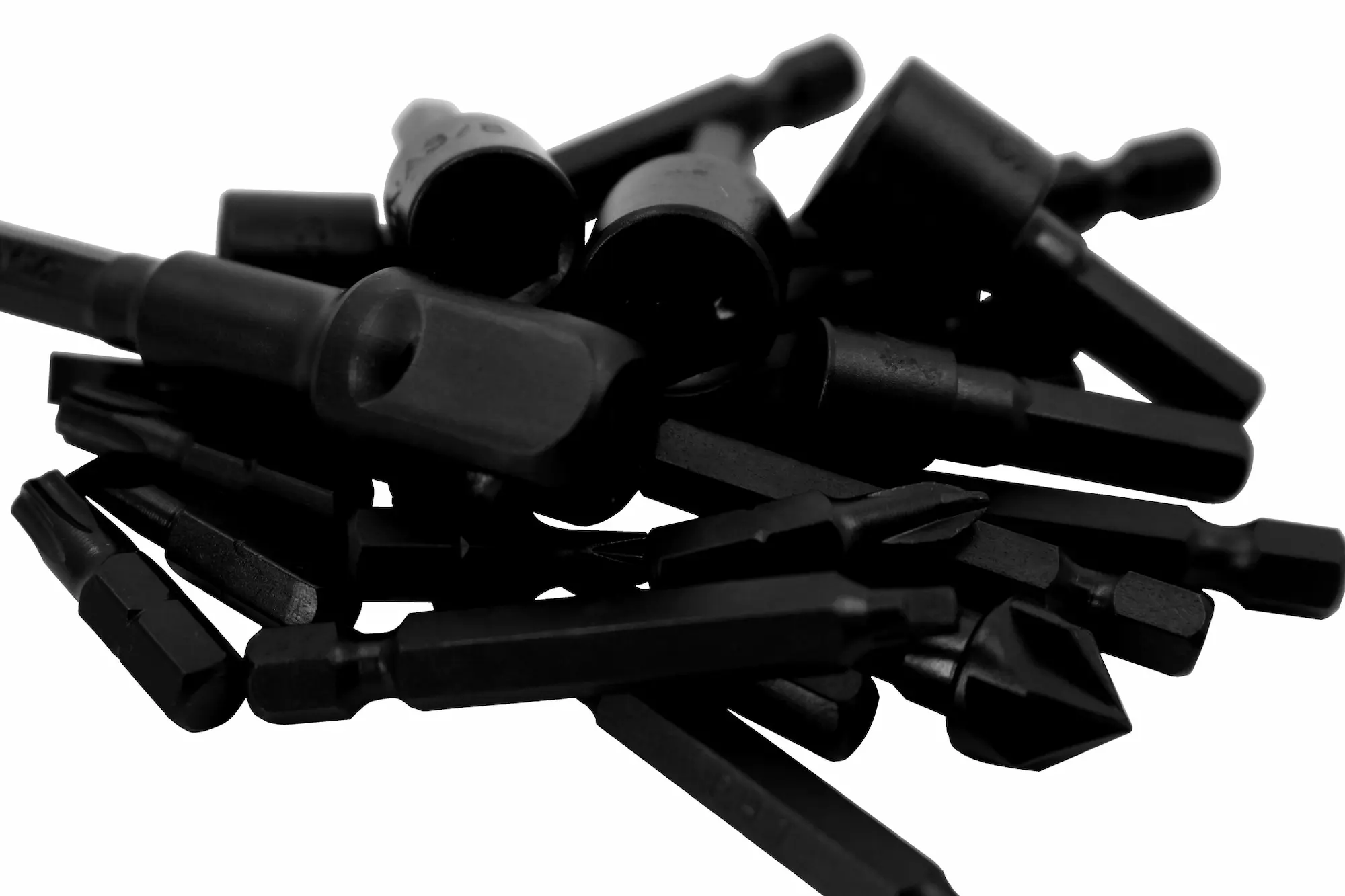
Introduction
In the evolving landscape of metallurgical advancements, Black Oxidizing stands out as a transformative process. This technique, primarily known for imparting a dark, protective finish to metals, plays a crucial role in enhancing both the aesthetic and functional qualities of metal components. Not only does it provide a sleek, decorative appearance, but it also significantly improves corrosion resistance. This article delves into the benefits and applications of Black Oxidizing, exploring its impact on various industries and the process that makes it an indispensable tool in metallurgy.
Embracing Black Oxidizing
Enhanced Aesthetics
Black Oxidizing offers a striking finish to metal parts, providing a sleek, sophisticated look that is highly sought after in decorative and consumer products. This elegant finish reduces light reflection, making it ideal for optical equipment and other applications where glare reduction is crucial.
Corrosion Resistance
One of the primary benefits of Black Oxidizing is its ability to form a protective oxide layer on the metal surface. This layer significantly reduces the risk of corrosion, extending the lifespan of metal components and ensuring their durability in harsh environmental conditions.
Applications in Various Sectors
Due to its dual benefits of aesthetic enhancement and corrosion resistance, Black Oxidizing finds widespread application across diverse industries. From automotive to aerospace, consumer electronics to military hardware, this process is integral in manufacturing parts that require both functional resilience and visual appeal.
The Black Oxidizing Process
- Cleaning: The process begins with thoroughly cleaning the metal components to remove any contaminants, ensuring an even and effective oxidizing treatment.
- Oxidizing Bath: The cleaned parts are then immersed in an oxidizing bath, typically a solution containing alkaline chemicals that facilitate the formation of the black oxide layer.
- Rinsing: After oxidizing, the parts are rinsed to remove any residual chemicals, ensuring a clean and consistent finish.
- Sealing: Finally, a post-treatment sealant is applied to enhance the corrosion resistance of the oxide layer and to improve the overall durability of the finish.
Conclusion
Black Oxidizing is not just a process; it's a significant enhancement to the metallurgical industry. By providing both a protective layer against corrosion and an aesthetically pleasing finish, it adds considerable value to metal components. This dual functionality makes it an essential process for manufacturers seeking to combine durability with design. As a leading provider of Black Oxidizing services, Nitrera Technologies stands ready to bring these benefits to your next project. Contact us to discover how Black Oxidizing can transform your metal components into both functional and visual masterpieces.
Q vs QP vs QPQ Application Table
(Standard process)
Polish + Quench
Reduces Friction & Adhesion by up to 60%
Black Oxide (Quench) for Corrosion Resistance & Aesthetics.
Nitriding can increase RA up to ~32µin (0.8µm) total
QP restores RA to ~8-16µin (0.2-0.4µm)
RA can be restored to ~2µin (0.05µm) by hand polishing or other means.
Some material may be aesthetically affected by brown/red iron oxides (particularly stainless steels and cast iron)
Very high quality & consistent appearance from part to part & batch to batch.
Polishing removes brown oxides and other surface contamination & visible defects.
(Compared to Raw / un-Nitrided Material)
Martensitic stainless steels: Moderate increase
Nodular irons: Slight increase
Precipitation hardened stainless steels: Unchanged
Ferritic & Austenitic stainless steels: Decreased
Martensitic stainless steels: Same as Q
Nodular irons: Same as Q
Precipitation hardened stainless steels: Reduced compared to Q
Ferritic & Austenitic stainless steels: Further reduced compared to Q
Martensitic stainless steels: Likely better than Q
Nodular irons: Same as Q
Precipitation hardened stainless steels: Likely better than Q
Ferritic & Austenitic stainless steels: Significantly better than Q
Components with high-spec aesthetic requirements. E.g.: Firearms, tools, etc.
Everything else if the additional cost is worth it.
1 55-60HRC for Carbon Steels, 60-70HRC for Low-alloy Steels, 70HRC+ for Stainless Steels
2 Nitriding is not expected to increase surface roughness (RA) where the starting roughness is >32µin (0.8µm)
3 Up to ~400hr ASTM B117 salt spray test